Once all the necessary components have been picked, we go into “steel and iron” with our experienced assembly team. The system setup is supported by the digital provision of the necessary system documentation. All processes are precisely planned and tracked as part of the Kurtz Ersa shopfloor management process. This ensures the transparency required to keep our customers up to date at all times.
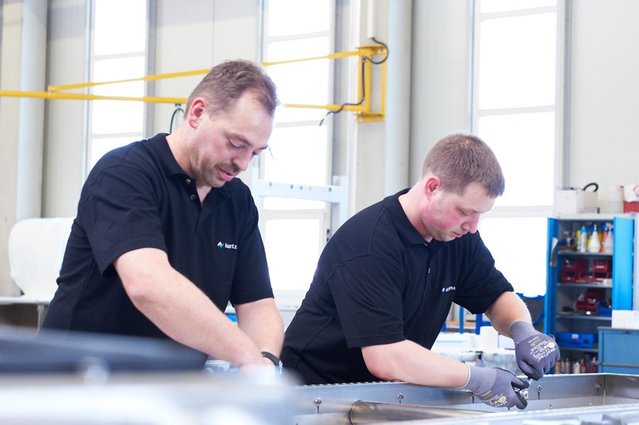
Commissioning incl. FAT / SAT
Once the assembly work is complete, the hardware and software are married. Our commissioning team breathes life into the automation system for the first time at one of our locations. As part of a test run, all the necessary system parameters are fine-tuned for the first time. After adjusting the mechanical and electrical interfaces, the main processes are fine-tuned and special process scenarios are integrated. After completing an extensive test run with documentation of the successful initial commissioning, we receive our customers for the Factory Acceptance Test (FAT). Of course, we then take care of dismantling, transportation to the customer's plant and reassembly of the automation system before our team recommissions the system at the production site in order to complete the final acceptance test (SAT) together with our customer.