Modular selective soldering platforms for entry-level to high-volume users
With innovative technology and modular design, Ersa meets the highest demands for flexibility and throughput - and still fits every budget. VERSAFLOW, SMARTFLOW and ECOSELECT are the successful Ersa selective soldering models. Benefit from the comprehensive expertise and wide range of services of the world market leader in selective soldering systems in your electronics production and find the ideal solution for your specific requirements together with the Ersa application experts!
In a class of its own - today and tomorrow Ersa Selective Soldering Technology
Selective soldering, the quality standard for THT components
With top technology and modular design, Ersa selective soldering systems meet the highest demands for flexibility and throughput - perfectly tailored to every need and every budget. A class of its own, a class for you!
In component manufacturing, selective soldering refers to the soldering of individual wired components onto printed circuit boards. The range of components usually includes components with low soldering heat resistance or dimensions that are too large for the SMD reflow process. Compared to classic wave soldering, the heat input into the assembly is significantly lower and solder masks are not required. By individually setting the soldering parameters for each solder joint, the process is characterized by the highest quality and reproducibility.
Process Steps Ersa Selective Soldering
Fluxing
Fluxing
The fluxing system of a selective soldering machine must fulfill several requirements at the same time. In addition to precision and speed, high-quality fluxing processes require a high degree of reliability. The PCB areas that are not wetted by the selective soldering waves must not be exposed to flux.
State-of-the-art multidrop flux heads from industrial inkjet technology are used for this purpose. The flux is not atomized, but applied in individual small droplets to previously defined areas. Ersa offers various options for flexibility, throughput and process reliability to meet a wide range of customer requirements.
Highlights/Options:
- Multidrop precision fluxer
- up to 4 spray heads possible
- 2 flux containers possible
- Continuous monitoring of the flux application
- 2 fluxer modules possible
Preheating
Preheating
During the preheating process, PCBs are heated homogeneously before they are transported to the soldering module. The aim here is to provide up to 50 percent of the heat energy using infrared bright emitters so that the printed circuit board is not heated in a shock-like manner when it comes into contact with the liquid solder.
Lead-free, multilayer and high-energy applications in selective soldering, as well as the desire to always operate with optimum cycle times, require a constant improvement in temperature performance. Particularly for assemblies with high soldering heat requirements, the correct activation of the flux is essential for optimum wetting of the solder joints in order to ensure good capillarity and thus solder penetration. To meet these diverse challenges, Ersa selective soldering machines can be equipped with up to five preheating modules and optional top heaters.
Highlights/Options:
- Infrared bottom heating, segmentable for higher throughput
- Various top heaters with full or partial convection
- Pyrometer for temperature monitoring and logging
- Heating surface can be adjusted by program
- Power convection for homogeneous heating
Mini-wave Soldering
Mini-wave Soldering
The basic version of mini wave soldering uses a single soldering nozzle that solders each solder joint in succession. This provides maximum flexibility combined with the highest quality, as the soldering parameters can be set individually for each solder joint.
Regardless of which selective soldering machine the customer chooses, there are no compromises when it comes to soldering technology. All Ersa selective soldering machines are equipped with an electromagnetic solder pump. This technology offers the advantage that the lack of mechanically moving parts means that only minimal dross is produced, making the pot extremely low-maintenance. The pump ensures an extremely constant flow rate and therefore offers a precisely and finely adjustable solder wave height. Dynamic process parameters such as solder level, solder wave height and solder temperature are continuously monitored and documented.
Highlights:
- maximum flexibility due to variable y- and z-axis
- Individually adjustable parameters for each solder joint
- 360° soldering, no preferred soldering direction
- no costs for tools
- no lead time
Multi-wave Soldering
Multi-wave Soldering
Selective soldering processes lead to economic success if the processes are precisely adapted to the applications and quantities. A very important factor in this context is productivity, i.e. the throughput of assemblies through the soldering system.
In practice, this is achieved using multi-wave soldering technology. At the heart of the soldering units are product-specific soldering tools with individually designed soldering nozzles that convey the solder simultaneously and precisely to the soldering points of the wired components. This enables soldering times of 2-3 seconds per assembly to be achieved, regardless of the number of components to be soldered. Selective soldering systems based on multi-wave technology guarantee the user a stable, reproducible selective soldering process with short cycle times.
Highlights:
- Short cycle time due to simultaneous soldering
- Process time independent of the number of solder joints
- Maintenance "on the fly" (2 soldering modules)
- Minimum distances to neighboring SMT components can be realized
- Best energy transfer due to continuous solder flow
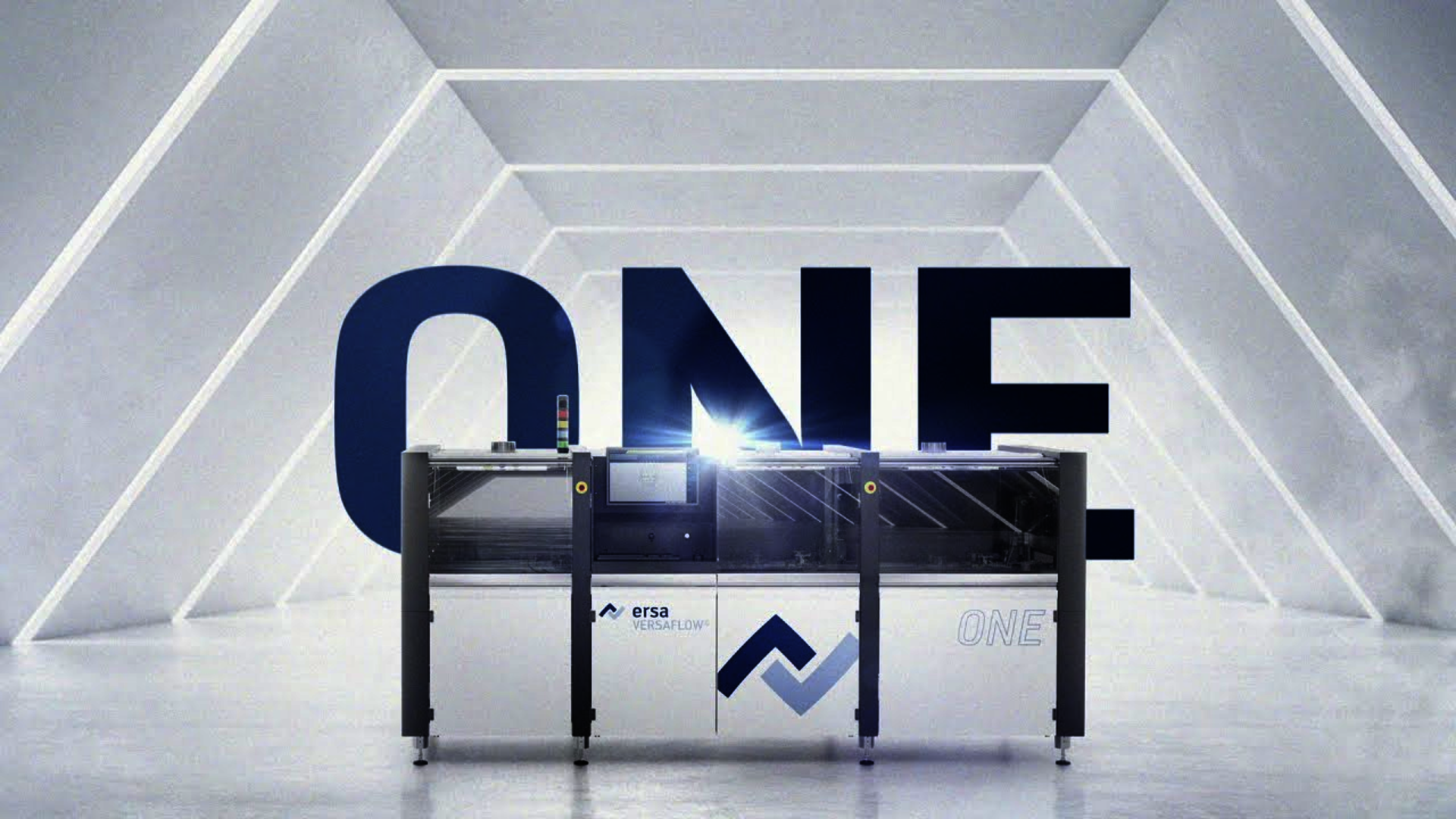
With the VERSAFLOW ONE, Ersa presents the entry-level model into the world of VERSAFLOW inline selective soldering machines. It incorporates decades of know-how from the market leader in the form of proven hardware and intuitive software.
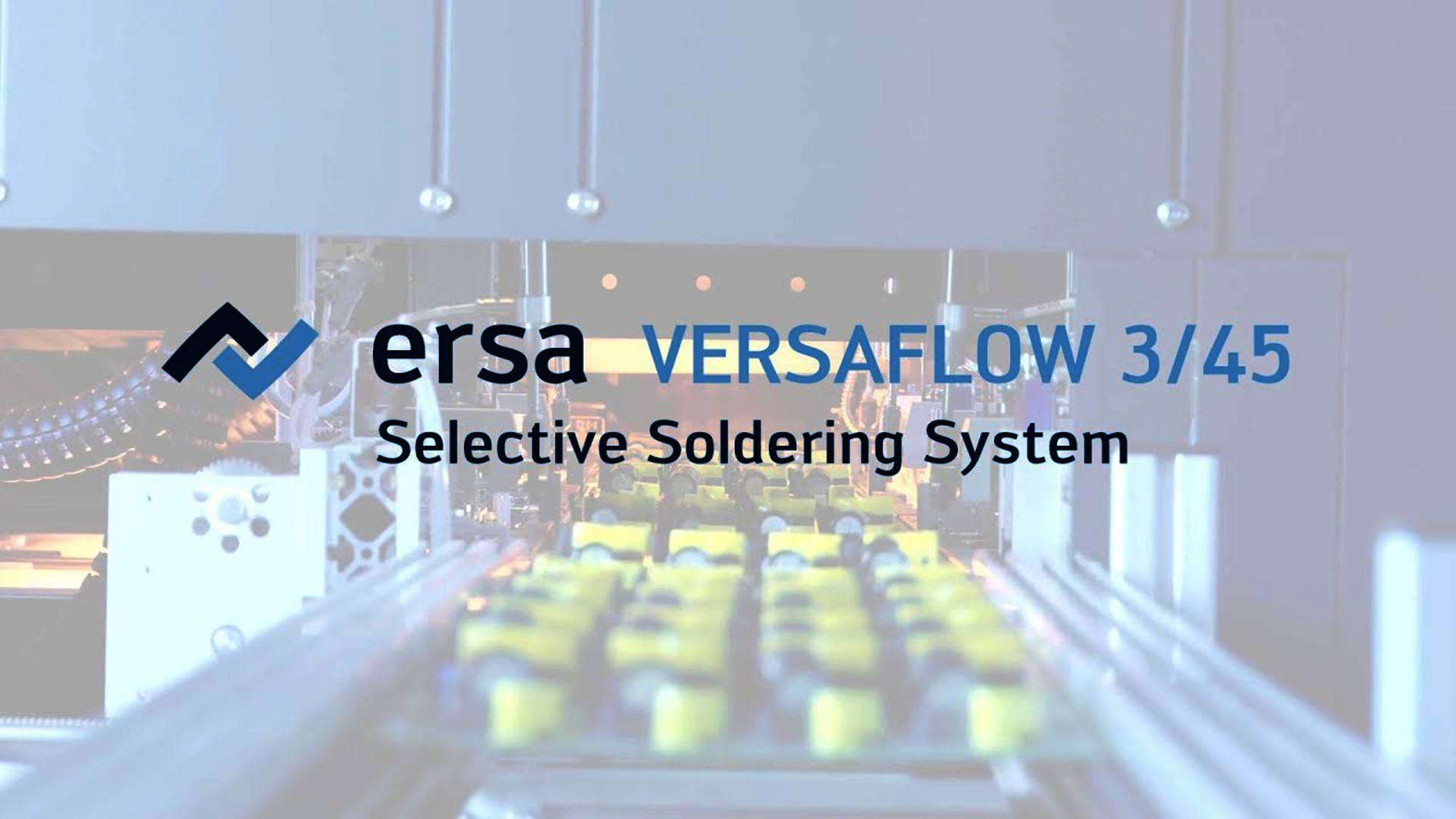
The VERSAFLOW 3/45 is the first inline selective soldering machine with double transport - it offers maximum flexibility and maximum throughput with minimum space requirements. Successfully in use over 2,000 times worldwide!
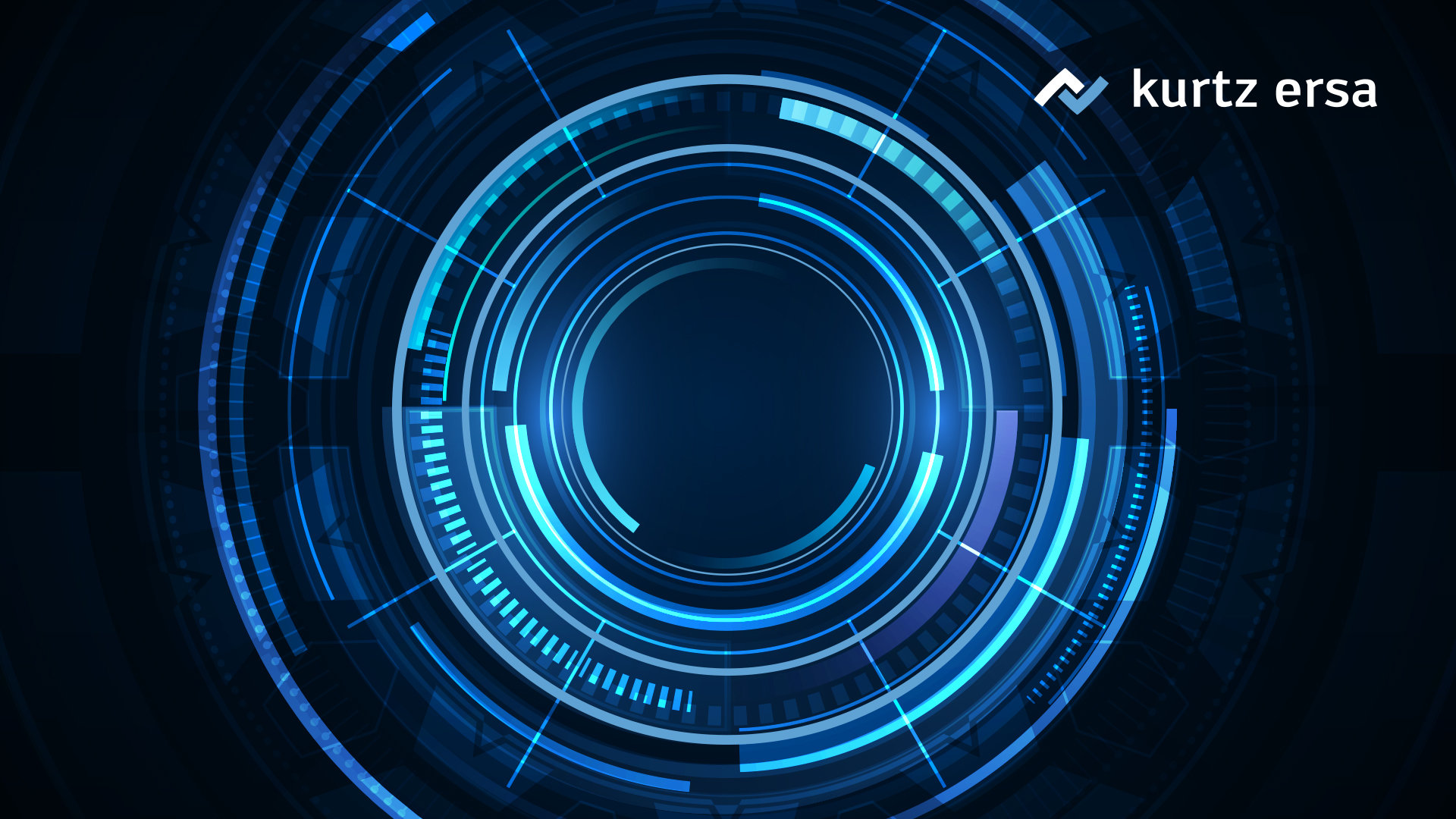
The best made even better and honored with the NPI Award 2016. VERSAFLOW 4, the latest generation of the world's leading inline selective soldering system, impresses with even greater process flexibility.